New robotic line at CIE LT Forge boosts production and quality with reduced manual labor
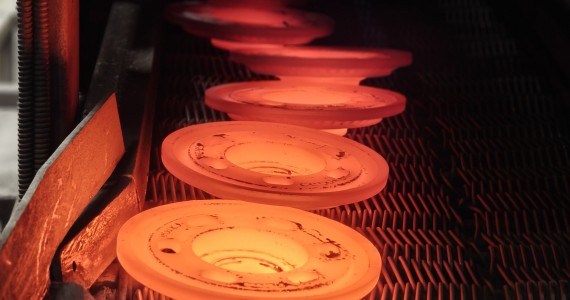
A new production line was recently robotized at CIE LT Forge in Marijampolė: this eases the physically demanding work for company employees while allowing for up to 30% more forged products and improved product quality. The total investment in line robotization and other improvements amounted to approximately 1 million euros.
The company has been on the path of robotization for several years
CIE LT Forge, the leader in automotive component forging in the Baltic states and a part of the international CIE Automotive group, had another record year in 2023. The company continued to increase its production volume and sales, reaching revenue of 55.7 million euros, which is 23% more than in 2022 (45.3 million euros).
Investments in modernization and robotization significantly contributed to the company's rapid growth and high performance. The company has been pursuing robotization for more than a decade, starting in 2011 when the first partially robotized line was installed in the Big Forging. Later, in 2018, a second line was implemented – this time fully robotized.
"The decision regarding the robotization strategy for the Small Forging was made in 2019. The main reason for this decision was to increase the company's competitiveness by automating key processes. The excellent results of the robotized line installed in the Big Forging in 2018 reinforced the decision that the direction was correct and technically feasible," shares CIE LT Forge CEO Darius Masionis.
Although three out of five lines in the Small Forging are robotized, with no decision yet on the robotization of the remaining two lines, Masionis emphasizes that such a combination has its advantages.
"The advantage of manual lines is greater flexibility, which is necessary when producing relatively small product batches. Robotized lines can produce these too, but their setup and launch time and costs would be disproportionately high. Therefore, the Small Forging now has great flexibility: large product batches are manufactured on efficient robotized lines, while trial and small batches are produced on manual lines," reveals Masionis.
Robotized lines produce up to 30% more parts
The CEO of CIE LT Forge says that robotization provides multiple benefits to the company: the line requires fewer operators, its productivity increases, and additional capacity becomes available for manufacturing new products.
"Operator working conditions have also improved, eliminating constant heavy physical labor. It's important to mention that product quality has also improved, as operators can focus on control, process monitoring, and management," lists Masionis, adding that robotized lines produce up to 30% more parts compared to non-robotized lines.
Speaking about what can be manufactured on the newly robotized Small Forging line, Masionis notes that all lines in this forge can produce similar products if there are no size limitations, regardless of whether the lines are robotized or not.
"Today, the lines produce various 0.7-12 kg forgings for the automotive industry. Usually, these forgings are blanks for further metal processing operations and, compared to other blank production methods, stand out for their high strength and optimal price, which is valued in various industrial sectors, especially in the automotive industry," says the CEO of CIE LT Forge, which manufactures steel components for automotive market giants such as Audi, Volkswagen, and Renault.
No fear of job losses
The implementation of technologies, where various devices can perform more tasks with minimal human intervention, may cause concern among employees whose positions are threatened by robotization. However, Masionis says that the company experienced the anxiety and apprehension phase back in 2018-2020 when two fully robotized lines were introduced.
"Today, employees have no fears. Everyone understands the benefits robotization brings to the company and the employees themselves – better working conditions, less heavy physical work, etc. Workers won’t be left without jobs because a robotized line cannot operate fully automatically – it needs to be adjusted, launched, and maintained," says Darius Masionis.
The company's efforts to work efficiently using the latest technologies have been recognized nationally. For the second consecutive year, CIE LT Forge has been ranked among the TOP 10 smartest industrial companies in Lithuania in the "Smart Industry" competition. This competition is organized by "Verslo žinios," the Lithuanian Confederation of Industrialists, and methodological partner EY.